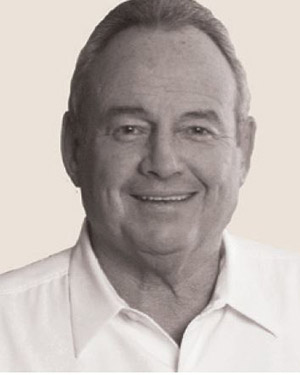
The $21 million, three-story, four-building residential complex in Palm Springs, Florida, built by Tom Murphy, Jr. and his company, Renco USA, based in Miami, doesn’t look unusual from the outside. Inside, however, its structure represents a potential revolution in construction, Murphy and others believe. Constructed entirely from a fiber-reinforced mineral composite construction system that uses blocks that interlock like LEGO bricks to form its structural walls, floors and roofs, the Palm Springs building is stronger than concrete and is rated to withstand winds of up to 275 mph.
Construction of the project, overseen by Coastal Construction Group, where Murphy is CEO, required a crew of just 11 workers with varying skill and experience levels to erect the three-story buildings using only manufactured materials, a proprietary adhesive and a mallet Bonded together by a methyl methacrylate binding agent, the construction system did not require heavy cutting, welding or masonry work. Murphy says the system is cost-competitive with both concrete and wood-frame construction.
The Palm Springs project was a long time coming. From the initial concept of creating a nested building block, the effort evolved into the development of a comprehensive building system. About a dozen years and 400 tests later, as the testing program sent them back to the drawing board to fine-tune the product, the Renco block system is now certified by the International Building Code, allowing the its use worldwide.
Stronger and stronger
The team spent all that effort “trying to get it approved,” Murphy says. “We had to keep changing it to make it better and easier to work with. When we did that, making a building with it became faster and easier, and… the building got stronger every time.”
Another advantage, Murphy notes, is that the system’s incorporated carbon is estimated to be 80% lower than steel and about 60% lower than concrete.
Ken Smuts, president of Renco, credits Murphy for seeing the effort through to completion, despite the long process, and for constantly seeing ways to improve the product. “Tom is a meticulous planner and has high expectations,” says Smuts. “His attention to detail is second to none. You need someone like Tom at the helm of this thing to get things going. He just perseveres.”
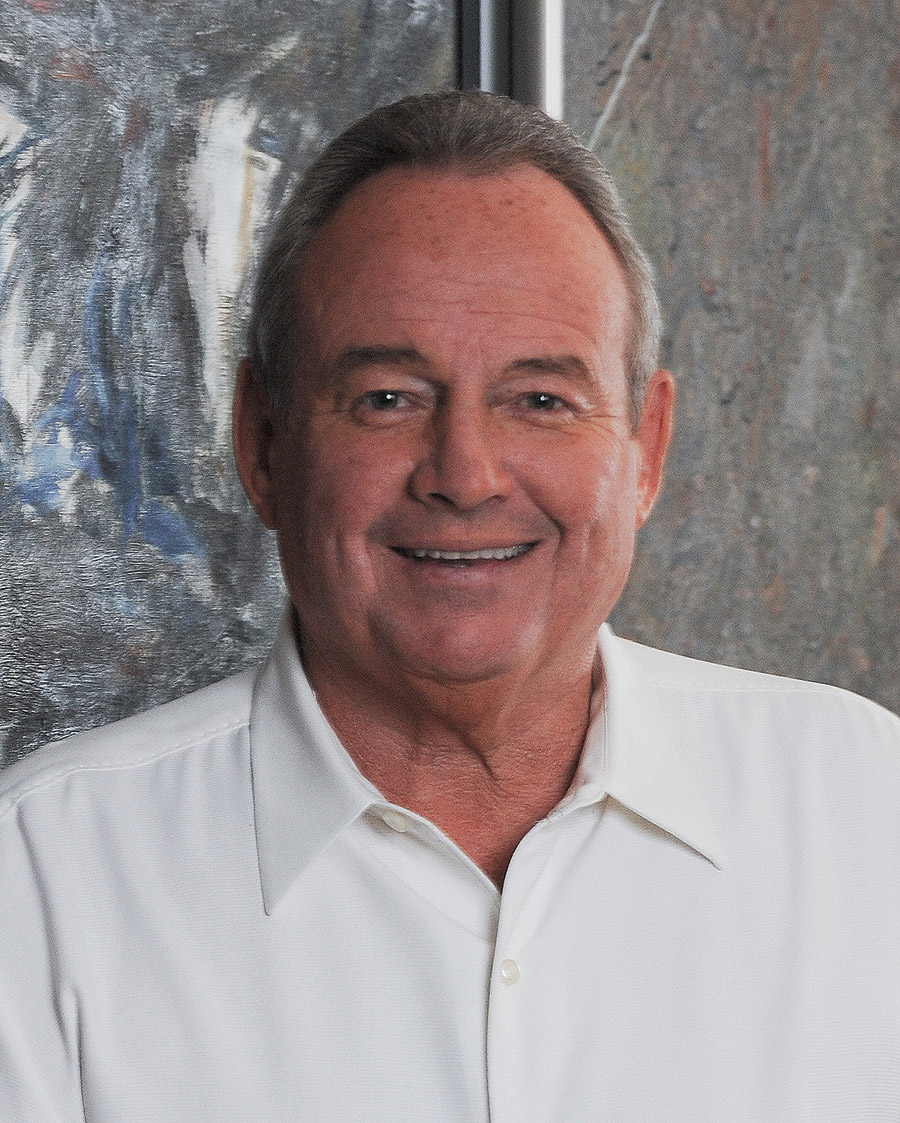
Tom Murphy Jr.
Photo courtesy of Renco Inc.
The journey through development, testing and certification challenged the resolve of the Renco team. “There are always setbacks, and Tom was the voice of reason for most of it,” says Smuts. Just as important, he adds, “Tom is a continuous communicator, he always pulls up and gets the job done. It’s 24 hours a day, 7 days a week and beyond. The guy is 75 years old and doesn’t stop.”
Among those who testify to the merits of the Renco system is Richard Wood, the former president and CEO of Plaza Construction, who saw it in person. Noting the ease of assembly of the system, Wood notes, “it not only opens up the opportunity to not have a quality control problem, but the strength of the material, the simplicity of it, the strength, the confidence in it once it’s mounted. … this is a game changer.”
Murphy hopes Renco can provide stronger, more affordable housing where it’s needed most. “This is a superior product that’s affordable, that can meet those needs quickly and efficiently,” he says. “That really excites me.”