This audio is automatically generated. Do us know if you have comments.
Since 2020, events have usually obtained a pre and post-paid label. This is true in construction.
For example, contractors had hoped that construction prices would return to pre-pandemic levels. However, five years after the start of the Covid-19 pandemic, the costs have not yet been reduced. In addition, construction professionals are Function to obtain another increase in the costs of the materials Due to the ongoing and nearby rates.
The virus that left the world changed indelible continues to affect the building industry as the calendar becomes on March 11, the date of 2020 that the World Health Organization declared Covid a global pandemic. The United States issued its own national emergency on March 13, and the states instituted lock orders shortly after.
“At first, we thought that the stop would only last a few months. And once people started returning to work in person, we thought it would take a few months to manufacturers to personalize and work through setbacks, “said Hiscoe, CEO of Shawmut Design and Construction, a general contractor in Boston.

The hiscoe
Permission granted by Shawmut
Hiscoe wasn’t alone in this thought. Following the prices for essential materials such as iron, steel, brick and switching change in 2020 and 2021-he reached the peak in June 2022 to 46.4% above the levels of February 2020, many contractors expected a gradual return to pre-paid levels, said Sharon Wilson Géno, President of the National Housing Council, Millichap Economic and real estate real estate and real estate webinar property at the beginning of the webinar at the beginning of the year.
But what increased has not really dropped.
“There was a post -concal expectation that construction costs would be reduced somewhere around the previous levels, but this has not really happened,” said Wilson Géno. “Although we have not seen the volatility in the prices of the construction we saw during Covid, it has been largely raised in most markets, but it is flat at a much higher level.”
Inputs to non -residential construction are now placed 40.5% higher in February 2020According to the price index of the producer. Much of this increase occurred in the years immediately after the appearance of pandemic. Since 2022, costs have increased largely Around the same level.
Materials costs jumped 40.5% since February 2020
PPI for contributions to non -residential construction, indexed to 100 in June 2010.
“The conditions of the supply chain have improved, and many suppliers reported more short availability and short waiting time,” said Rob Mineo, CEO of IMF Capital Advisors, an investment signature based in North Carolina. “However, although the situation has been standardized to some extent, there is no definitive metric to confirm a complete return to pre-pandemic conditions. Many operators continue to make team orders in advance as a precautionary measure against possible future interruptions.”
Shuffle of supply chain
Prior to Covid, the construction industry was very based on world -wide building manufacturers, said Dave Steffenhagen, an executive of the Mchugh Construction project, a chicago general contractor. In response to interruptions in the pandemic induced supply chain, companies like MCHUGH have developed more relationships with domestic and American material suppliers.
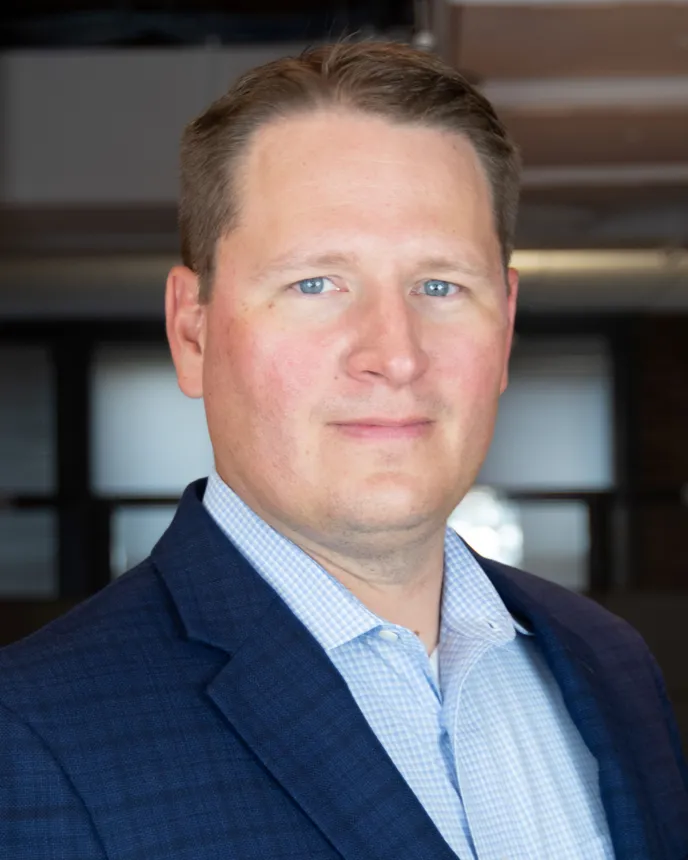
Dave Steffenhagen
Permission granted by MCHUGH CONSTRUCTION
“No one knew how long the delays of the supply chain of the material would last. It was an unsafe time that no one was ready, “Steffenhagen said.” Now, we can provide our customers multiple recommendations for alternatives equivalent to home products abroad. “
In addition to resorting to the manufacturers closer to home, federal spending also played a role in stabilizing the supply chains, said Mineo. The prices, which had been climbing at a fast pace, finally settled. The driving times of certain materials, such as asphalt, even improved after 2022, feeding the optimism that construction costs would gradually tend, said Mineo.
But this optimism has faded. By 2023 and 2024, construction prices were altered to still high levels, showing little sign of a significant fall. Now, three months by 2025 and five years after the fall of Calamity, contractors accept a new reality.
The prices do not stay high, they climb again.
Impacts
On March 4, President Donald Trump imposed a 25% rate on Mexico merchandise and most of Canada, along with an additional 10% rate on Chinese products. The Trump Administration on March 6 suspended these rates On all imports that comply with the United States-Mèxic-Canada agreement until April 2.
But on March 12, almost five years a day that Covid was declared a pandemic, the Trump administration plans to promote a 25% rate in all imports of steel and aluminum worldwide, as well as a 50% rate in Canadian metals.
Although these measures should not yet be pasted permanently, the threat of them has already affected the construction industry. Prices increased in January as Contractors rushed to buy materials Before possible deadlines.
It New rates “It will damage,” said Mark Zandi, a Moody’s Analytics chief economist during the Marcus & Millichap event.
Forecasting of the US Building Market
2020 | 2021 | 2022 | 2023 | 2024 | 2025 | 2026 | 2027 | |
---|---|---|---|---|---|---|---|---|
Building materials | 1.5% | 26.9% | 12.6% | -2.9% | -1% | 2.4% | 2.2% | 2% |
Construction machinery | 1.8% | 4.5% | 10.4% | 9.4% | 2.5% | 2.1% | 2% | 1.9% |
Source: Moca Systems
The United States is very based on imports of wood, steel and cement, making these materials especially vulnerable to pricing ascents, Brandon Michalski, a Moca Systems building economist, a Boston building consultant. In fact, Michalski provides for an increase in costs of 2.4% year -on -year construction materials by 2025, after a decrease of less than 1% by 2024.
In other words, while the next disposition has put contractors on a firmer ground than before Covid, the changes have not yet made North -Americans builders independent.
“There are risks in this perspective of rates related increases,” Michalski said. “United States trust in imports of wood, steel and cement products can significantly affect the cost of construction by 2025”.
The impact could be especially serious in cement and aggregates, Mineo said.
“North -American cement consumption has overcome domestic production in recent years, leading to a significant increase in imports,” said Mineo. “With the national production already capable, the highest import costs would also increase national prices, as producers would have little incentive to maintain low prices.”
For the aggregates, prices are expected to continue to increase constantly, but not at a rate of level of overtension, Mineo said. Most of the aggregate production in the United States is domestic, although some regions that are based on the imports of Canada and Mexico will have an impact, he added.
Margins are narrowed but without slowdown
The news comes at a time when The contractor’s benefit margins are already inAccording to a survey associated with builders and contractors. The costs of higher materials, combined with a scarcity of persistent labor, have been an additional tension to the budgets.
“With the exception of a black swan event, it is unlikely that construction costs will see significant decreases by 2025,” said Michalski.
However, the shovels continue to hit dirt within certain sectors.
It Project stress indexthat makes some delay clues and abandoned projects along with Construction begins dataIndicate that certain segments constantly maintain the highest costs. This suggests that developers are finding ways to move forward despite the expensive landscape, said Wilson Géno.
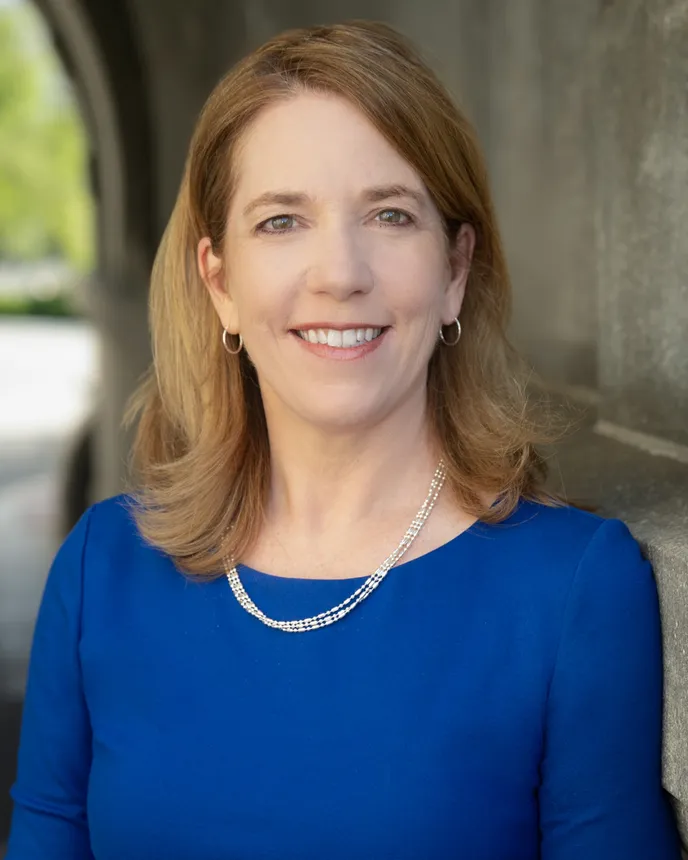
Sharon Wilson Géno
Courtesy of the National Multifamily Housing Council
“There are some anecdotal tests that some offers begin to move forward,” said Wilson Géno. “These offers have just been adjusted to the new environment, and they have found that, because demand continues, which could also find a higher cost.”
Michalski echoed this feeling, adding that, while some projects will be delayed or reduced, most developments are adjusted to a permanently higher cost environment. Data centers, for example, took into account more than 75% of the monthly gain of expense under construction In January, according to an analysis of builders and contractors associated with US census data.
“Although some projects may be pushed or canceled, the majority is expected to continue as companies adapt through value engineering and strategic planning,” Michalski said. “The industry is still resistant despite these challenges.”
Now, as the construction industry works during the fifth year since the start of the locked, the supply chain snarls and the scarcity of materials, the builders are preparing for the feeling of Deja Vu again.
“Inventory management has definitely changed; we are now operating in the new standard,” Hiscoe said. “The project configuration time is still much longer than the pre-pandemic days, so the collaboration and initial collaboration with clients, architects and engineers is essential.”