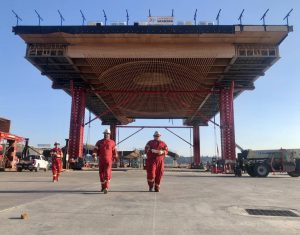
Recently, a heavy cargo solutions company helped install five different types of 20 roof panels at Portland International Airport (PDX), Oregon, as part of a terminal expansion project with the aim of doubling the size of the airport.
A key component of the expansion is the construction of a new seismically isolated roof structure in the central area of the airport. Mammoet was contracted to lift, transport and install the 20 roof panels avoiding disruption to passengers.
The roof, made mainly from locally sourced and sustainable wood, was completely prefabricated between the airport’s active runways over the course of a year. Before being moved, the ceiling panels were disconnected in pieces roughly the size of a football field to be transported to the new terminal extension. This allowed the airport to continue as usual while minimizing disruption to airport operations. Depending on the type of panel, each was cast, rolled into place, placed directly by self-propelled modular conveyors (SPMT) or lifted by crane to its final position.
Most of the panels were to be installed on top of the populated areas of the existing terminal building. With safety at the forefront of the entire project, work was done during strict overnight closures when the public could be kept away from the work area. Once it was verified that the area was free of pedestrians, the installation of the roof panels could begin. Each panel, called a super cassette, was installed using a stationary skid driven by wire jacks and lowered with the skid jacks onto column insulators. The next set of panels was rolled into position by the bottom flanges of the previously set panels. The panels were safely secured with the high wind potential and project-specific seismic requirements in mind before the public could re-occupy the area below.
Panels range in weight from 40 tons (36.3 tons) to 632 tons (573 tons), with dimensions up to 72 x 50 x 6 m (236 x 164 x 19.7 ft). Mammoet used four towers of its lifting systems to raise the roof panels to approximately 17 m (56 ft) to allow SPMTs with working falsework to be driven under each roof section. At midnight on the day of each move, the tracks were closed to 1.6 km/h (1 mi/h) panel transport from the moving yard to the terminal.
A major challenge was the wood material used in the construction of the roof panels. Deflection of the roof panels was a major concern of the client and roof designers, so at every point in the shipping, handling and installation process, roof deflection was controlled and kept within of strict criteria. Only the super-cassette pieces had steel girders in the longitudinal direction to support the 25 m (82 ft) wooden arches and to allow the panels to be “launched” by stationary skid equipment. Additionally, the jack stands were temporary towers supported by wooden piles that were installed in the 1950s.
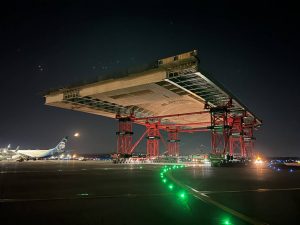
To mitigate any issues, Mammoet performed extensive friction testing at its Rosharon, Texas yard prior to execution to ensure that no structural damage occurred to a mock-up roof panel and that the design values presented to the client for the anchorage of the rope grip were realistic. On site, Mammoet closely monitored loads and deflections to ensure they were in line with tested values.
So far, Mammoet has successfully placed 16 panels to close the first phase of the project. Four additional panels will be installed during the second phase in 2024, after the client has built the interior of the new terminal extension for general occupancy. Mammoet’s airport-related experience includes examples such as the elevated pedestrian walkway at Seattle-Tacoma International Airport (SEA), the world’s longest air bridge in Hong Kong, and the transportation of buildings airports in Texas.