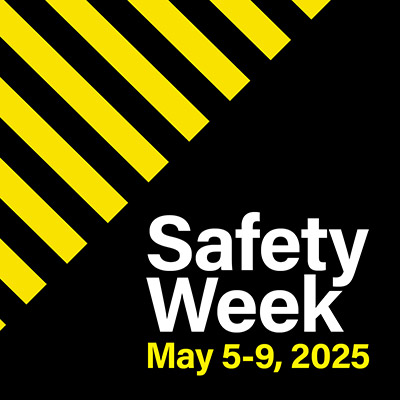
One night in September 2019, a crew of ten Electric Inc. He worked at the ground level of the Museum of Sciences and Griffin Industry in Chicago, updating the museum’s aging electricity system. Some of the electric infrastructure of the old building went back to a century.
The task that night, according to Osha records, was to eliminate and replace a splicing box on a vault at the museum’s floor level. It is used to hold heavy electrical bundles and sometimes made of steel, cast iron or porcelain, the boxes had to be climbed to the ground level to replace the wiring and connections. General’s Capatàs, John Kane, who had successfully removed four smaller joints during the previous months.
When Kane was in the controls of a power stacker, a type of lifting carrier walking behind, other crew members were in the vault of 3½ feet deep that maneuvering the straps around the forks and the spalling box. Kane released the bump, testified, and rotated the acceleration to remove the stacked truck from the vault with its useful load.
It was when the problem affected.
Instead of throwing the box up and out of the vault, Kane felt that the stacker was wounding to the edge of the open floor and saw him fall, fixing one of his crew members against the vault wall.
What happened pushed the Occupational Health and Safety Administration To cite and propose a fine against up to modify the stacker mistakenly through the pit and to expose workers to the dangers because Kane had never been trained to use this stacking model.
Thus electric, which is based on BroadView, ill., did not grant. The contractor answered the Osha’s initial penalty $ 23,868 for the two serious offenses, arguing his case in an audience before OSHA Administrative Law Judge, Brian Duncan, by 2022. The key problem revolved around whether Kane should have formed the specific stacker. He argued that Kane’s proven skill with similar equipment and their preparation and operation of the stacker test was sufficient.
Building accidents represent less than one in 20 of all the accidents in the United States each year, according to recent OSHA data, but buildings of construction forklifts represented one in four of the 67 fatalities in 2022.
On the night of the museum’s accident, a rescue was needed.
Firefighters Answer
Chicago Firefighters came quickly and started working to release the worker fixed by a lift trolley and the 6,800 pounds of machinery on top. According to television reports, the rescue team consulted the emergency doctors of the Chicago Medical Center, and the Firefighters were able to administer medicines against pain and stop their bleeding during the laborious extraction where a goal was not to cause more injury.
After 45 minutes, the Firefighters released the injured worker and transported him to the hospital with a forearm and a left elbow fractured that required multiple surgeries.
Then began a wider debate on the need for specific training of the machine.
The crew operation that night was different from several ways of the previous four times that the hun workers had removed the splicing boxes. First, the fifth box was heavier. Kane estimated its weight at about £ 1,000 depending on their experience, but in fact he weighed 1,370 pounds, a potentially critical factor. Ten usually, it was used by a rented pallet stacker for these lifts, but that day the machine was not available.
With the permission of the museum’s manager, Kane borrowed the Toyota 6bwc15 Toyota 6bwc15 Toyota 6bwc15 truck, an industrial truck (chest) with a capacity of 2,750 pounds. Kane had never operated this specific model earlier, although during his almost 30 -year career he had extensive experience with elevators, stacking trucks and pits. To prepare, he spent an hour on Friday reviewing the Toyota Stacker manual and, on the elevator night, conducted a brief visual inspection, recovering the stacker of his charging station on the second floor of the museum.
The lifeguards provided analgesic to the victim as they worked to release him from being trapped by an pocket. Photo: Chicago Fire Dept.
Kane testified that he had no idea why the stacker advanced instead of his back, speculating that it was a malfunction when he unexpectedly jumped and set the crew member against the opposite wall of the vault. The surveillance video confirmed that at 17:20 the stacker was stable, but at 17:25 the stackler was around the vault, the front wheels had crossed the edge.
Ten Electric denounced the incident in Osha that same day. Anton Stephens, the Health and Compliance Health Officer, spent three days reviewing the site, interviewing witnesses, inspects the stacker, taking measures and analyzing the surveillance images. His findings led to Osha to emit two serious violations. One was for an inappropriate workout for Kane and the other to make an unpayed modification of the stacker with lifting tapes. Unde challenged so much and Duncan, the Osha judge, dropped the summons of inappropriate modification.
However, he argued that Kane did not need formal formation in the battery because of being reasonably satisfied with the rules of the OSHA for the operation of fed industrial trucks. His lawyer cited numerous similarities between lifting and pallets, and Kane, although he acknowledged that there were differences in the capacity and loading of charge, he testified that he had operated pallets stackers not only for up, but during his previous work. According to Kane, in 2017, a pallets stacker was operating during the construction of an Amazon compliance center by a qualified coach who previously formed Kane in operation of forklifts.
Difference of opinion
Following a trial in November 2022, Judge Duncan dismissed the subpoena to illegally modify the stackler, but confirmed the violation of the training, saying that he did not assure Kane’s competition on the specific team, despite his experience with similar teams. Osha and uphill, which could not be made, then resolved and the contractor agreed to pay a $ 11,934 penalty.
There is very little Wiggle Room in the regulation of the Osha pit: entrepreneurs have to demonstrate competition in safe operation “as evaluated by the success of training and evaluation”. The training must combine formal instructions, such as conferences, discussions, reading and interactive instructions from the computer, with demonstrations of a coach and practical exercises. An evaluation is also needed.
David Smith, President of Alpine Engineering and Design in Utah, says that it is “absolutely reasonable in the rule to insist that a forklift operator is formed in the specific forklifts, no matter how much the experience has. Each manufacturer will do a little different.”
“The point of training.” Smith says, whose company serves as an expert testimony to lawsuits, “is that someone with more experience is there to see that you know the important parts and document that, in fact, you were given the information you need.”
“And the general rule is that without documentation,” he emphasizes, the necessary training “did not happen”.